How to implement ISO 9001 Quality Management System?
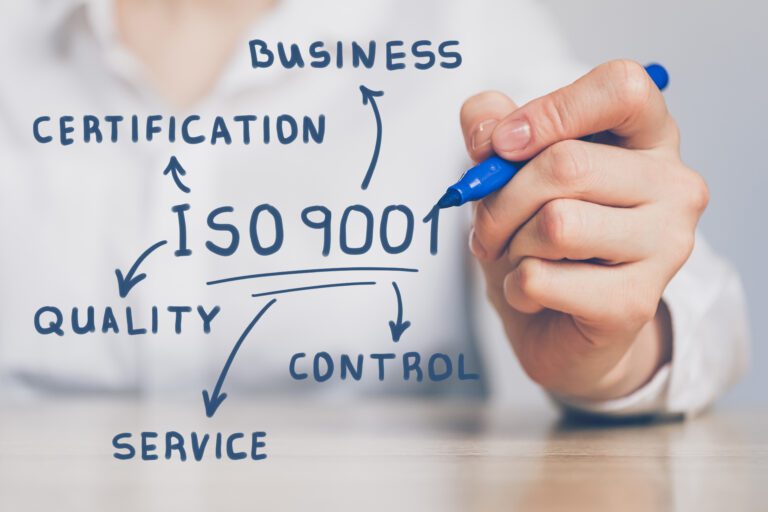
Implementing ISO 9001:2015 involves several steps to ensure your organisation meets the standard’s requirements for a quality management system (QMS). Here’s a comprehensive guide to help you get started:
1. Understand the Standard
- Read the Standard: Obtain a copy of ISO 9001:2015 and familiarise yourself with its requirements.
- Training: Consider training for key personnel to understand the standard’s principles and requirements.
2. Conduct a Gap Analysis
- Current State vs. Standard Requirements: Assess your current processes and identify gaps compared to the ISO 9001:2015 requirements.
- Document Findings: Document the areas where changes are needed.
3. Identify and Assign Management Support
- Top Management Involvement: Ensure top management understands the importance of the QMS and is committed to its implementation.
- Allocate Resources: Secure the necessary resources, including time, personnel, and budget.
4. Define the Scope of the QMS
- Scope Statement: Clearly define the boundaries of your QMS, including what is included and excluded.
- Document: Ensure the scope is documented and communicated within the organization.
5. Develop a Project Plan
- Implementation Team: Form a team responsible for the implementation process.
- Timeline: Establish a realistic timeline for the implementation process.
- Milestones and Objectives: Define key milestones and objectives.
6. Document the QMS
- Quality Policy and Objectives: Develop a quality policy and set quality objectives aligned with your organisation’s strategic direction.
- Processes and Procedures: Document processes, procedures, and responsibilities.
- Document Control: Implement a system for managing documents and records.
7. Implement the QMS
- Training and Awareness: Train employees on the QMS and their roles within it.
- Process Changes: Implement necessary changes to processes and procedures.
- Communication: Ensure effective communication throughout the organisation.
8. Internal Audits
- Audit Plan: Develop an internal audit plan to regularly review the QMS.
- Conduct Audits: Perform internal audits to ensure the QMS is effectively implemented and maintained.
- Corrective Actions: Address non-conformities and implement corrective actions.
9. Management Review
- Regular Reviews: Conduct regular management reviews to assess the performance of the QMS.
- Continual Improvement: Identify opportunities for improvement and implement necessary changes.
10. Prepare for Certification
- Choose a Certification Body: Select an accredited certification body to conduct the external audit.
- Pre-assessment Audit: Consider a pre-assessment audit to identify any remaining gaps.
- Certification Audit: Undergo the certification audit conducted by the chosen certification body.
11. Maintain and Improve the QMS
- Ongoing Monitoring: Continuously monitor and measure the performance of your QMS.
- Continual Improvement: Focus on continual improvement based on audit findings, feedback, and performance data.
Tips for Successful Implementation
- Engage Employees: Involve employees at all levels to foster a culture of quality.
- Simplify Documentation: Keep documentation simple and relevant to avoid bureaucracy.
- Focus on Customer Satisfaction: Align your QMS with customer needs and expectations.
- Utilise Technology: Use software tools to streamline documentation, monitoring, and reporting processes.
Implementing ISO 9001:2015 can significantly enhance your organisation’s quality management practices, leading to improved efficiency, customer satisfaction, and continual improvement.